Formply is Australia’s top choice for specialised formwork plywood, designed specifically for the demanding needs of concrete construction projects. This high-performance material has become an essential part of the Australian building industry, where precision and durability are crucial.
Choosing the right formwork materials is critical to the success of any construction project. The decision you make will affect:
- The quality of the concrete finish
- How efficiently the project timeline is managed
- How well construction costs are controlled
- The integrity of the structure
- The safety standards for workers
Formply stands out from other options due to its unique combination of strength, durability, and versatility. Its phenolic coating and cross-laminated construction create a superior surface for concrete forming, while its moisture-resistant properties ensure consistent performance in Australia’s varied climate conditions.
The material’s exceptional reusability factor and ability to deliver smooth concrete finishes have made it the trusted choice for builders across residential, commercial, and infrastructure projects. These characteristics, coupled with its compliance with Australian construction standards, position Formply as the benchmark for formwork solutions in the building industry.
Understanding Formply and Its Role in Australian Construction
Formply Australia is a specially designed engineered wood product made specifically for concrete formwork applications. This high-performance plywood has multiple layers of cross-laminated timber veneers glued together with phenolic adhesives, making it a strong material that shapes and supports concrete while it sets.
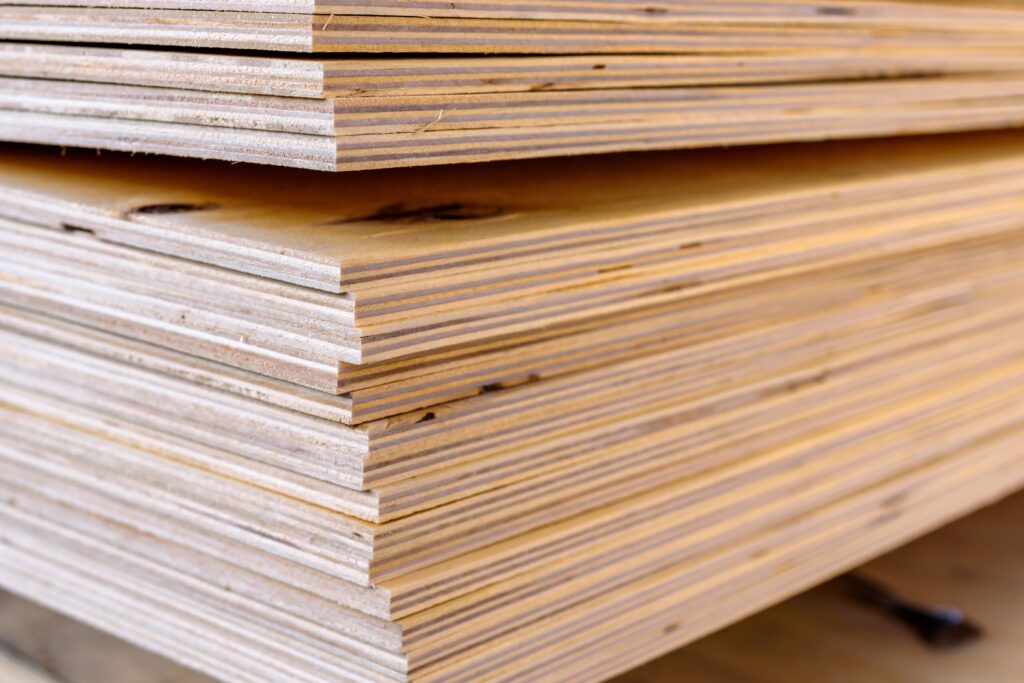
Primary Uses of Formply in Australian Construction
Formply is primarily used in Australian construction for:
- Vertical Wall Systems – Creating smooth, uniform concrete walls with minimal surface defects
- Horizontal Slab Formation – Supporting concrete floor and ceiling installations
- Column Construction – Shaping precise cylindrical or rectangular concrete columns
- Precast Element Production – Manufacturing standardised concrete components off-site
Key Differences Between Formply and Standard Plywood
Unlike regular construction plywood, Formply has unique features that set it apart:
- Film-faced surface coating for clean concrete release
- Enhanced moisture resistance through specialised treatment
- Higher structural integrity for repeated use
- Superior edge sealing to prevent water absorption
The way Formply is made also makes it different from regular plywood:
Read more at: Choosing the Right F17 Grade Plywood for Concrete Formwork
Standard Plywood Formply Basic wood veneer layers | Cross-laminated engineered layers |
Limited moisture resistance | Advanced water-resistant treatment |
Variable surface quality | Consistent, smooth finish |
Single-use applications | Multiple concrete pours capability |
These special qualities make Formply an important part of Australian construction projects where accurate concrete work requires dependable formwork solutions.
Key Attributes That Make Formply Ideal for Builders
The unique design of Formply makes it an excellent construction material with several important features that improve its performance on building sites.
1. Cross-Laminated Construction
The cross-laminated structure consists of multiple wood layers arranged perpendicular to each other. This strategic layering creates exceptional dimensional stability, preventing common issues like:
- Warping under temperature changes
- Bending under heavy concrete loads
- Twisting during moisture exposure
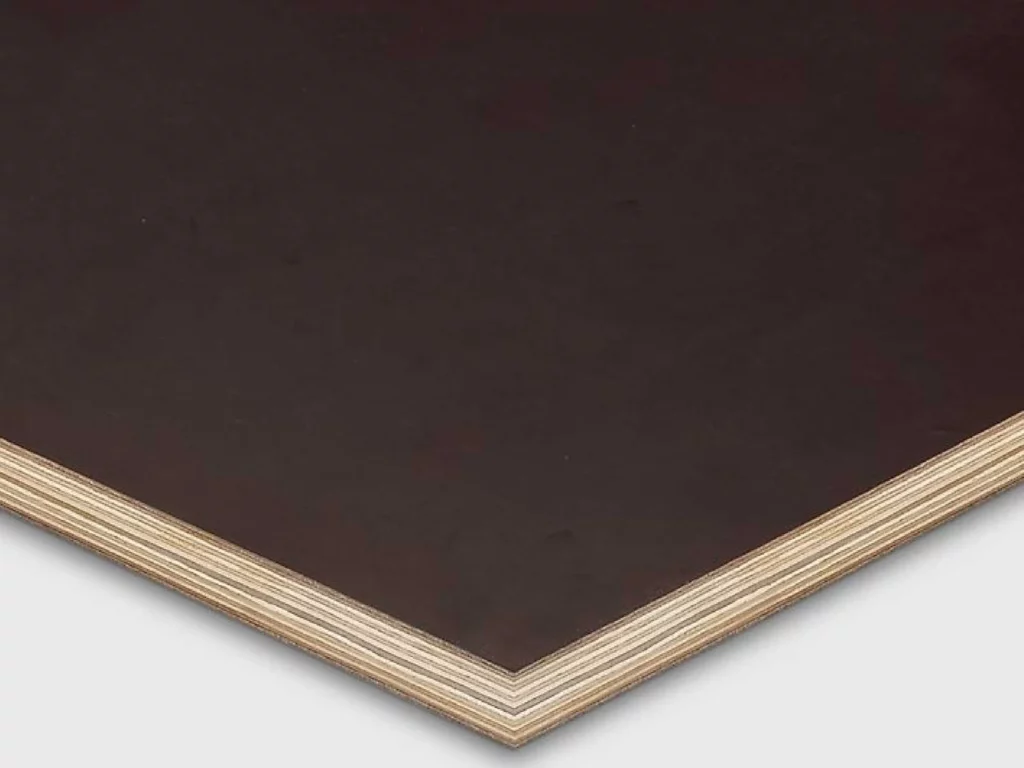
2. Advanced Adhesive Technology
The phenolic “A” bond adhesive forms an impenetrable barrier against moisture infiltration. This waterproof bonding system:
- Maintains structural integrity in wet conditions
- Prevents layer separation during repeated use
- Extends the material’s serviceable lifespan
3. Protective Surface Treatment
A super phenolic film coating applied to both faces provides comprehensive protection:
- Resists abrasion from concrete pouring
- Withstands chemical exposure from release agents
- Protects against impact damage during handling
- Creates smooth concrete finish quality
4. Health and Safety Benefits
The manufacturing process prioritises workplace safety through:
- Low formaldehyde emission levels
- Minimal volatile organic compounds (VOCs)
- Reduced respiratory irritants
- Safe handling characteristics
The phenolic surface treatment also reduces cleaning time between pours, allowing faster turnaround on construction sites. This protective layer maintains its effectiveness through multiple concrete pours, delivering consistent results throughout the material’s service life. Find more about formaldehyde on https://twu.edu/health-safety/chemical-hygiene-planlaboratory-safety/formaldehyde/
Stress Grades and Size Options Tailored to Project Needs
Formply’s versatility stems from its range of stress grades designed to meet specific structural demands. The three primary stress grades – F14, F17, and F22 – serve distinct construction requirements:
F14 Grade
- Entry-level strength suitable for basic formwork applications
- Ideal for residential construction and light commercial projects
- Cost-effective option for non-load-bearing structures
F17 Grade
- Mid-range strength perfect for standard commercial construction
- Enhanced load-bearing capacity for walls and suspended slabs
- Balanced combination of strength and economic value
F22 Grade
- Premium strength rating for heavy-duty applications
- Essential for high-rise construction and infrastructure projects
- Superior load-bearing capacity for critical structural elements
Standard Formply sheets come in two primary dimensions:
- 1200mm x 1800mm
- 1200mm x 2400mm
The typical thickness of 17mm provides optimal stability and strength for most applications. This standardisation allows builders to:
- Plan material requirements accurately
- Reduce waste through efficient cutting patterns
- Maintain consistency across large-scale projects
Selecting the appropriate grade depends on specific load-bearing requirements, project scale, and budget considerations. Higher stress grades command premium prices but deliver enhanced structural integrity and durability for demanding applications.
It’s also crucial to consider safety regulations during construction. The OSHA standards provide guidelines that can help ensure a safe working environment when handling materials like Formply.
Durability and Performance Under Harsh Conditions
Australian construction sites present challenging environments for building materials, yet Formply demonstrates exceptional resilience against these demanding conditions. The phenolic film coating creates an impermeable barrier, protecting against moisture penetration and preventing delamination – a common issue with standard plywood products.
During concrete pouring operations, Formply exhibits superior resistance to:
- Chemical attack from alkaline concrete mixtures
- Physical abrasion from aggregate materials
- Hydrostatic pressure from wet concrete
- Impact damage during placement and vibration
The moisture-resistant properties stem from its specialised manufacturing process:
The combination of high-density phenolic surface treatment and cross-laminated construction creates a robust defence against water ingress, maintaining structural integrity through multiple concrete pours.
The durability of Formply extends beyond basic moisture protection. The surface treatment provides enhanced resistance to: To read more about moisture click here.
- UV radiation exposure
- Temperature fluctuations
- Chemical spills
- Mechanical wear
With proper maintenance practices, Formply panels maintain their performance characteristics through multiple uses. Regular cleaning after each pour, correct storage practices, and careful handling protocols preserve the protective surface coating. This attention to maintenance translates into consistent concrete finishes and reduced material replacement costs across construction projects.
The robust nature of Formply makes it particularly suitable for exposed formwork applications where weather conditions can rapidly deteriorate lesser-quality materials. This inherent durability allows construction teams to maintain project schedules regardless of challenging weather conditions.
Sustainability Credentials of Formply
Formply’s environmental credentials stand as a testament to Australia’s commitment to sustainable construction practices. The manufacturing process adheres to Forest Stewardship Council (FSC) certification standards, ensuring responsible forest management and ethical timber sourcing.
Key Environmental Benefits:
- Renewable resource utilisation
- Reduced carbon footprint
- Sustainable forest management
- Minimal waste production
- Local ecosystem preservation
The integration of Laminated Veneer Lumber (LVL) formwork with Formply creates a powerful combination for eco-conscious construction. This pairing reduces the need for steel-based alternatives, resulting in decreased carbon emissions during production and transport.
Formply’s sustainability extends beyond its raw materials. The product’s durability enables multiple reuse cycles, minimising waste and reducing the demand for new materials. This characteristic aligns with green building certification requirements, contributing valuable points to projects seeking environmental ratings.
Australian builders implementing Formply contribute to:
- Decreased landfill waste
- Lower transportation emissions
- Reduced energy consumption
- Enhanced biodiversity protection
- Improved air quality on construction sites
The product’s low formaldehyde emissions support healthier work environments while meeting strict Australian environmental regulations. This combination of sustainable sourcing, efficient use, and environmental compliance positions Formply as an essential component in Australia’s green building revolution.
Cost-effectiveness Through Reusability and Longevity
The economic advantages of Formply extend beyond its initial purchase price, making it a cost-effective choice for Australian builders. A single sheet of high-quality Formply can be reused 15-20 times when properly maintained, creating substantial cost savings across multiple projects.
The durability of Formply translates into direct financial benefits:
- Reduced replacement costs: The robust phenolic coating prevents concrete adhesion, minimising damage during stripping
- Lower labour expenses: Less time spent on form preparation and maintenance between pours
- Decreased material waste: Extended lifespan means fewer purchases and disposals
The lifecycle cost analysis reveals significant advantages:
- Initial investment: $75-85 per sheet
- Cost per use: Approximately $4-5
- Comparable single-use alternatives: $20-25 per application
These figures demonstrate how Formply’s reusability creates substantial savings, particularly for large-scale projects requiring multiple concrete pours. The material’s resistance to warping, delamination, and moisture damage ensures consistent performance throughout its service life, protecting the builder’s investment while delivering reliable results.
Complementary Products Enhancing Construction Outcomes
The integration of complementary construction products with Formply creates a robust building system that maximises structural integrity and site safety.
Reo Bar Installation
- Precise reo bar placement ensures optimal concrete reinforcement
- Strategic spacing prevents concrete segregation
- Rust-resistant options extend structure lifespan in coastal areas
- Proper tie-wire securing prevents displacement during concrete pours
Chain & Shade Mesh Protection
- 50% coverage mesh suits general site protection
- 90% coverage options ideal for dust control
- UV-resistant materials maintain long-term effectiveness
- Sound dampening properties reduce urban construction noise
- Essential protection for workers and materials from weather elements
LVL Formwork Integration
- High-strength engineered wood complements Formply systems
- Vertical and horizontal applications increase structural stability
- Reduced material requirements lower project costs
- Enhanced load-bearing capacity for complex concrete forms
- Superior dimensional stability in varying weather conditions
The combination of these elements with Formply creates a comprehensive construction system that delivers superior results while maintaining safety standards and cost efficiency.
Best Practices for Storage, Handling and Maintenance of Formply
Proper storage and handling practices significantly impact Formply’s performance and longevity. The following guidelines ensure optimal condition maintenance:
Storage Requirements
- Store sheets flat on level ground with adequate support
- Keep sheets elevated from ground contact using timber bearers
- Maintain protective covering against rain and direct sunlight
- Place sheets in well-ventilated areas to prevent moisture build-up
- Stack sheets horizontally with aligned edges to prevent warping
Handling Guidelines
- Use mechanical lifting equipment for large sheet quantities
- Carry individual sheets vertically to prevent bending stress
- Implement two-person lifting techniques for manual handling
- Avoid dragging sheets across rough surfaces
- Protect edges during transport and placement
Maintenance Protocols
- Clean surfaces after each concrete pour
- Remove residual concrete using plastic scrapers
- Apply release agent before each use
- Inspect sheets regularly for signs of damage
- Repair minor surface damage promptly
- Sand rough spots between uses
Moisture Protection
- Check moisture content before use (ideal range: 8-12%)
- Store under shelter during wet weather
- Address water pooling immediately
- Maintain proper site drainage around storage areas
- Use moisture-resistant covers during extended storage
These practices protect Formply’s structural integrity and surface quality, maximising its reuse potential and ensuring consistent concrete finish quality across multiple applications.
Industry Impact and Builder Preferences in Australia
The rising costs of building materials in Australia’s construction industry have changed how builders make purchasing decisions. Now, builders are prioritising materials that last longer and can be reused multiple times, making Formply an affordable solution in tough market conditions.
Quality Assurance Standards
Quality assurance standards have become extremely important when builders choose their materials. Australian builders consistently opt for Formply because it offers:
- Reliable performance across various project needs
- Smooth surface finish in concrete applications
- Consistent strength characteristics from one batch to another
- Proven compliance with Australian Standards
The Role of Suppliers
The role of suppliers is crucial in maintaining these quality standards. Covert Procurement demonstrates this through:
- Strict quality control processes
- Direct relationships with certified manufacturers
- Efficient supply chains that reduce cost variables
- Technical support for optimal material selection
The Importance of Supplier Expertise
Market analysis shows a strong link between builder satisfaction and supplier expertise. Suppliers who keep comprehensive stock levels of different Formply grades enable builders to:
- Access materials that meet specific project requirements
- Reduce procurement delays
- Maintain project timelines
- Control construction costs
The combination of rising material costs, quality assurance needs, and supplier capabilities continues to strengthen Formply’s position as a preferred construction material in the Australian market.
Conclusion
Formply is Australia’s top choice for construction formwork, offering exceptional value with its combination of durability, versatility and cost-effectiveness. Its ability to withstand harsh weather conditions, high reusability potential, and consistent concrete finish quality make it an invaluable asset for builders across the country.
The product’s comprehensive benefits align perfectly with Australia’s demanding construction requirements:
- Structural integrity – Cross-laminated layers and phenolic coating ensure reliable performance
- Environmental responsibility – FSC certification supports sustainable building practices
- Economic efficiency – Extended service life reduces long-term project costs
- Safety compliance – Low formaldehyde emissions protect worker health
- Quality assurance – Standardised manufacturing creates dependable results
These qualities make Formply the logical choice for Australian builders who want to maintain high construction standards while effectively managing project costs. Its proven track record in delivering superior concrete forming solutions continues to reinforce its status as the preferred formwork material across the Australian construction industry.